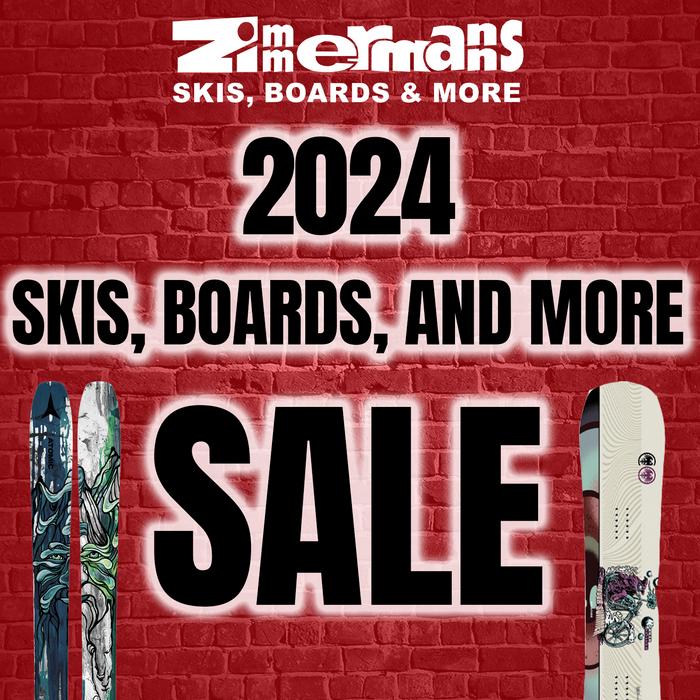

Interview With a Ski and Snowboard Tech: Kyle Stankard | Zimmermanns Skis, Boards, and More
Hey whats up Kyle, go ahead and introduce yourself!
Kyle: Hey! My name is Kyle Stankard, lead tech over at Zimmermann's Skis, Boards, and More. I've been tuning skis for about five years now. I have been snowboarding my entire life and grew up right here on the east coast.
Whats your favorite go-to snowboard right now?
Kyle: My favorite board right now is probably my old Rome Garage Rocker. Just a flat true twin style board. In my opinion a pretty underrated style, something that a lot of guys who are advanced riders aren't really on these days. Everyone has moved on to some of the new hybrid shapes, which are awesome, but there is something to be said for that flat-camber profile, they're pretty versatile... or I should say more versatile than what some other guys are saying out there.
What are some main things you look at when checking in tune-ups?
Kyle: The first thing I do when customer brings in their skis is I take a good look from tip to tail, up and down. Top-sheet, base, looking for minor imperfections or major scratches, gouges, or anything that can be found on the ski (or board). Checking the ski to see if it still has any base structure left, that way I can find the right package or recommendations to get them back out on the hill and having fun. Sometimes some of these fine details are hard to notice, especially for a customers who aren't too familiar with ski maintenance. They might notice a big core shot or major top-sheet damage, but often times there are detrimental aspects to their gear.
Any recent examples?
We recently had a customer bring in a ski that up-front, didn't really look all that bad. I noticed that right underfoot there was a small bubble, come to find out after cutting it out we found that his edge had split all the way through (through the base). That can obviously be catastrophic for the ski and we try to be upfront with expectations on what can be repaired, but I try to do my best and usually they come out really great. We also try to be transparent on how long some repairs may last, because sometimes repairs on gear that is close to a total loss can be more of a "band-aid".
What do you like about being a ski tech?
Kyle: Taking a ski or board that should be a complete loss, or working with someone coming in who is super discouraged saying "hey man I hope you can do something with this" and they are expecting the worst. Then we take their gear and we fix it up really nicely and get them back on the hill with a repair that was done beautifully. Just seeing the look on their face when they say "Wow, how did you fix that?" That's where I take a lot of pride in my job and what I do. Especially in the case where a customer can get back out skiing or riding without needing to buy new gear that they might not be able to afford.
When one of the guys approaches me saying "hey Mr. Kyle I got this gnarly core shot and it is looking #$%^*%^ terrible". Every time Im going to tell them we can fix it, or at least do our best. Working on these challenging projects and sharing the results with the customer is just really awesome and something I enjoy.
Any tips on taking better care of your skis or board?
Kyle: Okay, I think one of the number one things I find when customers bring their gear in is that they've stored them somewhere where they probably shouldn't have. Whether that be out in their shed all season and you find that the tails of the skis are completely rusted all the way through. If they stored them in their attic, or the loft in their garage where gear can get bent or warped from changes in temperature over the summer. The best thing to do is to store your gear in a cool, dry place like anything you would put in dry-storage.
Another thing that I see a lot is customers may not be good at keeping up with waxing their skis or board. We see a lot of really dry bases coming in the shop. That's definitely another thing, along with the whole storage thing. We have seen people who will leave their skis up on their Thule rack for the season! (laughs) After the day of skiing is over, they go up on the roof where they will live for the winter. Please don't do this, the salt from the road will ruin your gear (Jerry of the day). Clean them off when you get home and keep your gear dry to help prevent rusting.
Thoughts on tuning robots?
Kyle: I think there is still a lot of value there (hand tuning). Personally I am still warming up to the whole robot thing. I am definitely an advocate for good craftsmanship and attention to detail with a sharp eye and steady hand. I think that is one aspect required in getting a solid, bullet-proof tune. Not to say that the robots can't product a good, consistent tune, because they absolutely can. In my opinion there is nothing that can replace an a good craftsman who is used to having their hand and eyes on the product and can find those fine little details that could be missed by someone just operating a machine.
So the robots are just essentially another tool for a great tech to use?
Kyle: The robot is absolutely a tool. It does not replace a good tech at a ski shop. In many industries, machines and advances in AI have been replacing jobs and I was a bit worried when I learned about it moving into the ski industry. After having quite a bit of experience with the new machines, I don't think they will be taking jobs away from the industry. You still absolutely need someone there to have their hands and eyes to manage the quality and consistency being produced. The robot that we use from Wintersteiger does produce some absolutely stellar tunes, but just like any human, mistakes can be made. While I do believe that a well trained tech can produce an incredible tune, tuning robots have increased efficiency and improved our overall consistency on all of our tunes.
What do you like about working at Zimmermann's?
Kyle: My favorite part about working here is probably the teamwork, the comradery you know. We are definitely a fine tuned, oiled machine. We need everyone to come in and operate this ship every single day. We have such a stellar group of people here that really help that work, it's awesome. Its great to see everyone working on the same page, like "hey man lets get this done today, lets make things happen" and all work together to keep the skiers and riders in our area happy out on the slopes. I think we do a great job at that.
Want to hear more about our tune ups? Check out our services at zimsport.com
Leave a comment